About Sead
Sead Dedovic is an experienced Director of Operations with a suite of continuous improvement focused skillsets: budgeting, capital expense management, general operations, P & L oversight, management, retail operations, manufacturing, and production. Sead specializes in executing continuous improvement initiatives in the food manufacturing industry. He has experience in the following food manufacturing categories: bakery, poultry, sauces, soups, entrées, and sandwiches. Moreover, his twenty-plus years of high-level leadership is guided by his extensive training in quality and safety processes: Lean Six Sigma, HACCP, SQF, and PCQI. As a proven Kaizen and Gemba leader, he has continuously empowered work forces in order to develop first-tier managers. Sead's methods and management style also make him an effective manufacturing executive in both union and non-union environments.
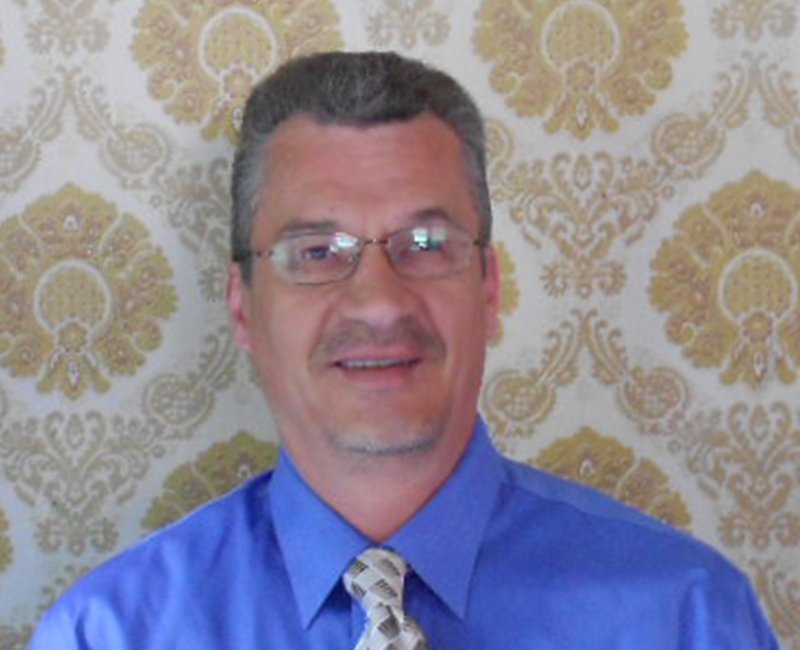
Note: Sead Dedovic is pictured wearing a blue shirt. (New York, NY · 2016)
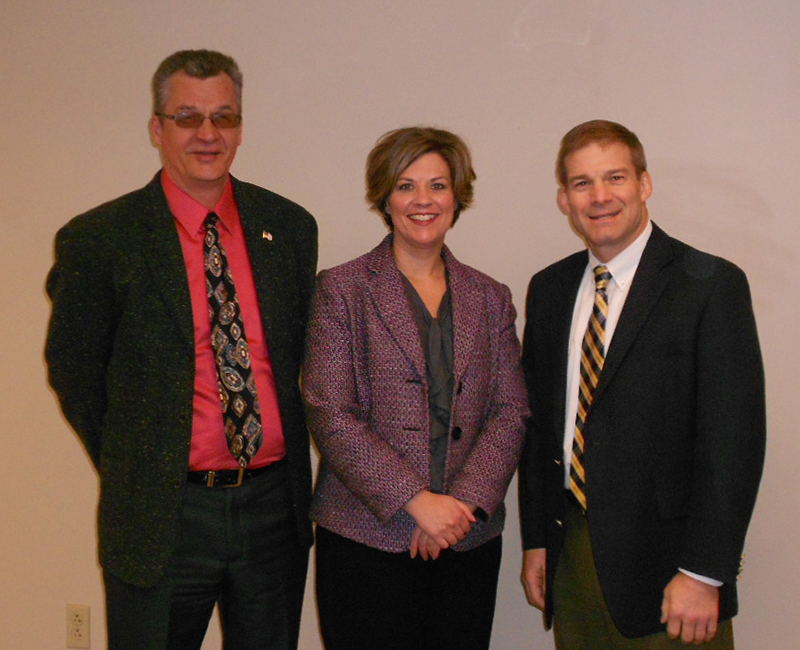
Note: Sead Dedovic is pictured wearing a black suit and red shirt alongside Tisha Livingston and U.S. Congressman Jim Jordan. (Amherst, OH · 2013)
Core Capabilities
Sead's core capabilities encompass over twenty years' worth of experience in various food manufacturing facilities, locations, management teams, and regulatory environments. His commitment to world-class leadership and operational excellence was thoroughly demonstrated during the COVID-19 pandemic. While at Hale and Hearty Soups in Manhattan, NY, Sead worked closely with senior leadership in order to adapt quickly. He initiated creative solutions, minimized employee dissatisfaction, and executed quickly–even though New York City was one of the most challenging regulatory environments to negotiate in the entire nation.
Process & Safety
- Lean Six Sigma
- SQF
- HACCP
- PCQI
Food and Manufacturing
- Frozen poultry
- Baked goods
- Soups and dressings
- Retail restaurants
Regulatory
- FDA and USDA
- Unions
- State guidelines
- OSHA
Management
- Kaizen and Gemba
- Mentoring
- Staffing agencies
- Continuous improvement
Professional Experience
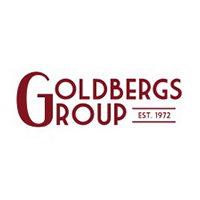
Director of Manufacturing
Goldbergs Group
Goldbergs Group is the premier food solution provider of restaurants, manufacturing plants, commercial kitchens and airline catering solutions. I was accountable for the production of cabin meals for all Atlanta airport flights. This included breads, muffins, pastries, croissants, Danish buns, biscuits, etc. We also sold our products to retail, foodservice, and wholesale customers.
- Duties: implement Lean Six Sigma best practices to increase efficiency and control labor costs
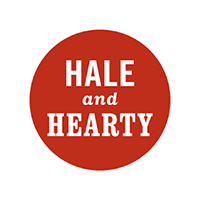
Hale and Hearty Soups LLC
July 2017 – October 2022 · Manhattan, NY · haleandhearty.com
Hale and Hearty Soups is a privately held company that operates twenty-seven retail restaurants and two manufacturing plants that produce soups, sauces, dressings, and some baked goods.
Vice President of Plant/Retail Operations
Accountability entailed oversight and performance of the entire restaurant chain, wholesale sales, and two unionized manufacturing facilities. My direct team included two Plant Managers and one District Manager. Plants were unionized facilities.
- Duties: oversight and performance accountability of the entire restaurant chain, wholesale sales, and two manufacturing facilities
- During COVID-19: demonstrated gradual build-up from complete shut-down to make all locations operational within four months
- Implemented level III SQF system, and developed a total program for recertification
- Reduced DL cost by 8% via redesign of company operations
- Increased sales revenue by 14% via development and implementation of a novel business plan to promote profitable wholesale and retail channels
- Successfully implemented Lean Six Sigma across the entire organization
Director of Plan Operations
Managed two unionized manufacturing facilities with a near-total employee headcount of 250 people.
- Duties: oversight of entire manufacturing P&L
- Successfully negotiated a bargaining agreement with the Brooklyn facility's union leaders
- In 2017, successfully blocked union entrance to twenty-five restaurant locations in Manhattan, NY
- Through 2018–2019, effectively led manufacturing and played an active role in positioning the company for a sale
- Reduced operating costs by 22% despite the state's 33% salary-wage increase over a three-year period
- Reduced overall labor costs by $1.6M annually
- Developed groomed younger members of the leadership team to excel in in union environments
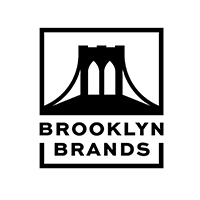
Vice President of Operations
Brooklyn Brands LLC
Brooklyn Brands is an artisanal baked goods manufacturer of various cookies, macaroons, rugelach, babka, and tarts. These goods are sold to the retail, foodservice, and wholesale markets. I was accountable for all baking operations in the Brooklyn, NY, facility. All facilities were FDA, CRC, OU, and Kosher regulated, with a 300+ total employee headcount. The manufacturing facilities also supplied the local Hasidic market and large national accounts such as Trader Joe’s, Costco, BJ’s, and others.
- Effectively managed TIR at 0 level
- Increased volume and revenue 27% without additional capital
- Conducted acquisition assessments for two facilities in Bronx, NY, and Newark, NJ
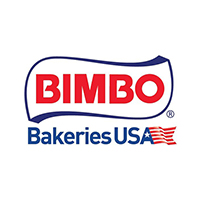
Consultant (Operation Portfolio Transformation Manager)
Bimbo Bakeries (Heiner's brand)
Bimbo Bakeries USA produces some of America's favorite bread, bagels, buns, English muffins, and sweet baked goods brands. Bimbo also operates baking facilities.
- Duties: provided consulting services to improve efficiency of bakeries in both West Virginia and Kentucky; responsible for implementation of manufacturing transformation in a union environment (RWDSU#21)
- Highlights: Increased weekly average EBITDA by 9.8%; increased gross margin by SKU to 27% – 32%; Achived a labor-to-sale-dollars ratio of 24%; increased customer fill-rate to 99.6%
- Achieved zero OSHA reportable injuries
- Increased material efficiency by 5% to 83.75%
- Improved line efficiency by 4.9% to 94% (#1 in the USA)
- Increased management's morale and efficiency via strategic initiatives
- Restored and improved relationships with four key customers
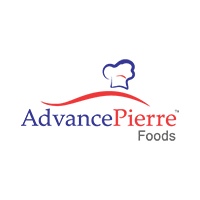
Plant Manager
AdvancePierre Foods
AdvancePierre Foods is a leading supplier of value-added protein and hand-held convenience products to foodservice, school, retail, club, and other markets. AdvancePierre's Amherst location is a 117,000 sq./ft. RTE/USDA/FDA regulated sandwich production facility with an annual operational budget of $24.5MM. AdvancePierre Foods was acquired by Arkansas-based Tyson Foods, Inc. in 2017 (read more).
- Duties: accountable for all plant operations, including budget development, P&L projections, and Lean Six Sigma implementation
- Highlights: reduced TIR from 6.84 to 1.98; reduced customer complaints from 4.6/MM to 0.5/MM; stabilized fill rate to 98.7% with 3.6 WOS; increased OEE to 3.5%/quarter; reduced COGS on plant level to $0.17/lbs.; reduced turnover from 112% to 17% annualized; reduced worker compensation claims to less than under $100/claim
- Conducted acquisition assessments for two facilities in Bronx, NY, and Newark, NJ
- Coordinated and oversaw all manufacturing, maintenance, purchasing, warehousing, and scheduling through significant production ramp-up from 20MM to 45MM lbs. of sandwiches
- Successfully implemented second shift production; developed and led installation of four new production lines, new plant KPIs, and created important partnerships with staffing agencies to support the growing plant's labor needs
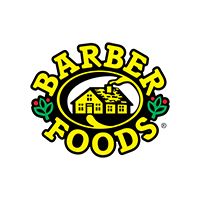
Barber Foods
2005 – 2010 · Portland, ME · barberfoods.com
Since 1955, Barber Foods of Maine has been producing America's favorite stuffed chicken breasts and other chicken products. During my tenure, the 120,000 sq./ft. manufacturing facility reached a total headcount of over 900 employees. Barber Foods was acquired by Ohio-based AdvancePierre Foods in 2011 (read more).
Plant Manager
Barber Foods
- Duties: accountable for all plant operations, including budget development and Lean Six Sigma implementation
- Reduced costs by 8% via improvement to processes
- Implemented $14MM automation improvements in packaging
- Actively assisted senior management during acquisition by AdvancePierre Foods
Superintendent
Barber Foods
- Duties: accountable for some plant operations, particularly with respect to process improvement via development and implementation of Lean Six Sigma initiatives
- Timely delivered $2.5MM annual savings while managing one DMADV; implemented four DMAIC projects with annual average savings of $418,000
- Developed and initiated forty-two Kaizen events with average savings of $45,000 per event
- Reduced direct labor from 620 to 280 employees while increasing output by 12%
- Earned Lean Six Sigma Black Belt and Lean for Manufacturing Master Black Belt
Background
Education, Certifications, and Awards
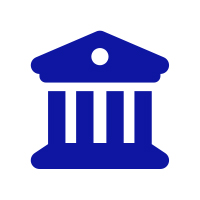
University of Bosnia & Herzegovina
Bacherlor's in Political Science
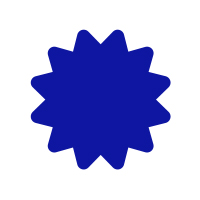
Certifications
- Certified Lean Six Sigma Black Belt
- Certified SQF Practitioner
- Certified HACCP Practitioner
- Certified PCQI Practitioner
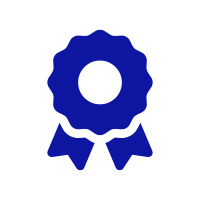
Awards
- 2012 Paul Allen Award – Operational Excellence
- 2011 Gus Barber Award – Product Innovation
- 2008 Barber Foods Award - Process Improvement
- 2006 Ron Marion Award – Cultural Development
Personal
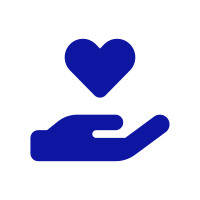
Supported Causes
- Wounded military veterans
- Armed forces of the United States of America
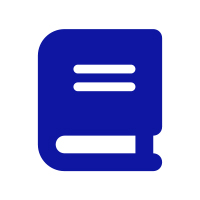
Influential Books
- Good to Great: Why Some Companies Make the Leap...And Others Don't by James C. Collins
- Built to Last Successful Habits of Visionary Companies by James C. Collins and Jerry I. Porras
- The Peter Principle: Why Things Always Go Wrong by Raymond Hull
Contact
Summary
Sead Dedovic is an experienced, highly-qualified manufacturing executive currently open to an exciting new employment opportunity in the Georgia or New England area. He has a proven track record with respect to his leadership capabilities, technical knowledge, and management style. He previously ran manufacturing facilities in New York, Maine, West Virginia, and Georgia; as a result, he has deep experience in negotiating challenging regulatory environments: federal, state, local, and union-friendly. Sead is a certified practitioner of Lean Six Sigma and other important operational methodologies.